This weekend I spent a lot of time working on a project I’m excited about: new speakers. These speakers are not for myself, they’ll be a birthday gift for my little brother, but still! Building loudspeakers is something I’m definitely passionate about, although this is the first time I’m mentioning it on the site. So let’s get into it!
First of all, why is this cool? Well, a ton of reasons. Building speakers is an art of trade-offs. There is, and never will be such thing as ‘perfect’ speakers. Every system is a compromise in some sense, with strengths in some areas and weaknesses in others. For example, the two main strengths in the ones I’m making right now are a high efficiency rating of 91dB (pretty good! This means that given less power, these speakers play louder than most), and a very smooth frequency response. The smooth frequency response was my main goal; important because my brother is going to recording school. If he’s going to be using these to audition recordings and potentially do mastering, it’s critically important that they don’t add their own ‘color’ to the sound. Speakers with choppy response curves can still sound great, but they add their own personality to the tone, which does not copy over to any other stereo setup. So it would be a terrible idea to master a recording on a system with a response curve that has lots of peaks and valleys. The weaknesses would be that I maybe didn’t get as deep of a bass response as I would’ve wished, and the price went a little higher because I insisted on drivers with good responses. In order to try to keep the costs down but still use good components, I omitted a midrange and used only two drivers per channel. For the enclosure, I chose to use a port to get what bass I could. I’d prefer a sealed box, but again, these are the compromises that you get forced into making. It’s part of what keeps it interesting.
There’s also the brand name aspect too. Just like having your favorite sports team or buying new shoes from your favorite brand, getting speakers from a particular maker is sort of exciting in and of itself. This time around I picked a tweeter from a Danish brand I’ve always wished I could afford, Scan Speak. Scan Speak is very highly regarded in the industry, and with that awesome pedigree comes an accompanying price tag. I’m guessing the recent economic downturn led them to eschew their typical snobiness and produce a series of drivers ‘for the people’ called their “discovery” series. Maybe it’s called that because it’s my opportunity to “discover” what it’s like to listen to Scan Speak (on the cheap)? This I look forward to.
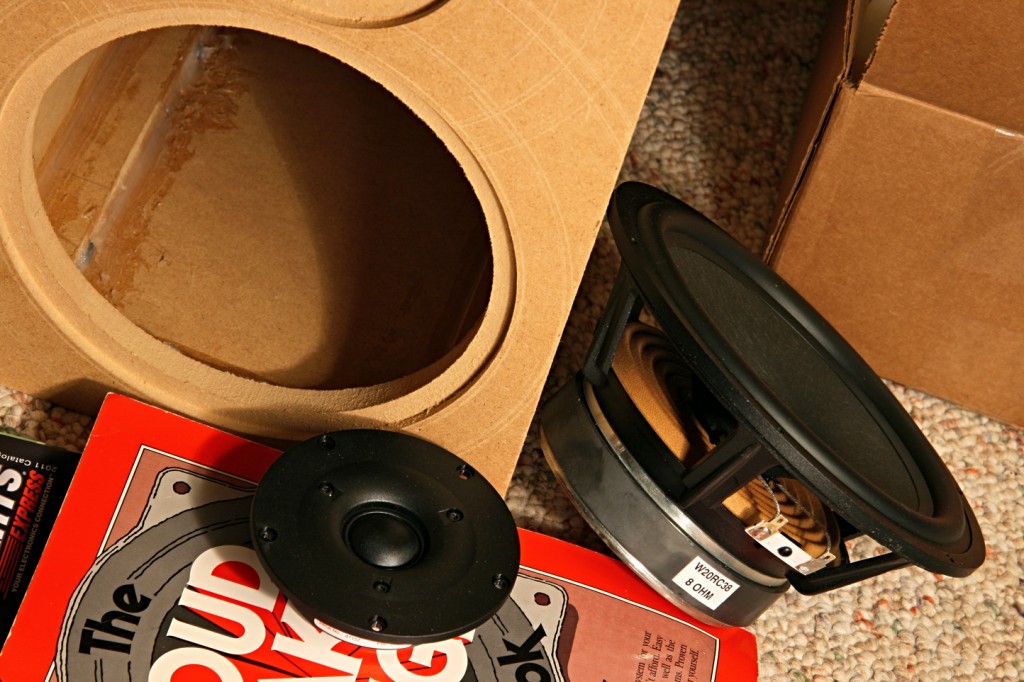
Something else very neat about speaker building is how long lasting it is. I built myself a pair in high school, and with one driver replacement (right midrange went bad) they’ve been serving me faithfully ever since. That’s well over a decade of listening. GOOD listening! I built another set for my buddy Luke, probably over a decade ago as well. Not long ago he told me he’s still lovin’ them and they continue to serve as his main listening system. That’s so rad! It brings me joy to think about this; the construction that I’m setting in motion in my garage today will last for decades. These are long term actions right now.
And more than that–these things will be making MUSIC! There will be huge moments of rocking out, when you’re getting ready to go do something great and you put on some tracks to pump yourself up! There will be mellow times late in the night when you come home and put on some chill vibes before you wind down for bed. Sad songs for when you just need to wallow in despair for a while, or daily anthems to get you into the groove of doing what you need to get done. These things are mood machines. Life enhancers. Tone establishers. Music colors our lives, it shapes our feelings. All those emotions will be flowing forth from these paper cones and cloth domes. I love that idea. LOVE IT!
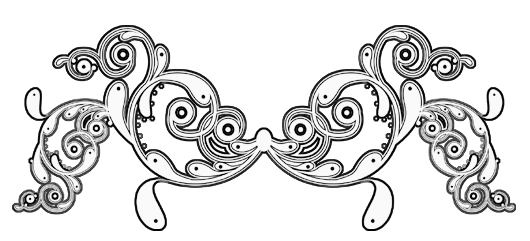
In the morning, I cook myself an omelet with red onion, cheddar, and spinach. Filled up and ready for action, I head out to the garage. The sun is searingly bright and as I step out, I hear a crescendoing rumble in the sky. Before I can even step out onto the driveway, I say to myself aloud, “what the hell IS that?!” As I pass under the garage door I look up and see one of the biggest propeller planes I’ve ever seen flying very, very low overhead. It’s a 4-engine passenger plane, like one of those vintage prop-airliners from the 60s or something. Very unusual, and a pitch-perfect start to the day. It’s like a good omen. I watch it lumbering slowly across the sky in a wide arc as it turns toward the nearby municipal airport, slipping away behind the treeline.
Making speakers is something I love doing so much that if I could choose one thing to do for the rest of my days, building speakers would be near the top of the list. While I was out in the garage, I thought back to Geoff Marcy and his story of picking what he wanted to do with his life. Things weren’t going good and he knew he had to make a decision to go in a new direction. He thought, well, what I really want to do is find planets even though it seems like a crazy idea. There’s really no money, glory, or fame in it, but I just want to do this because that’s what makes me happy. I could say the same thing about speakers.
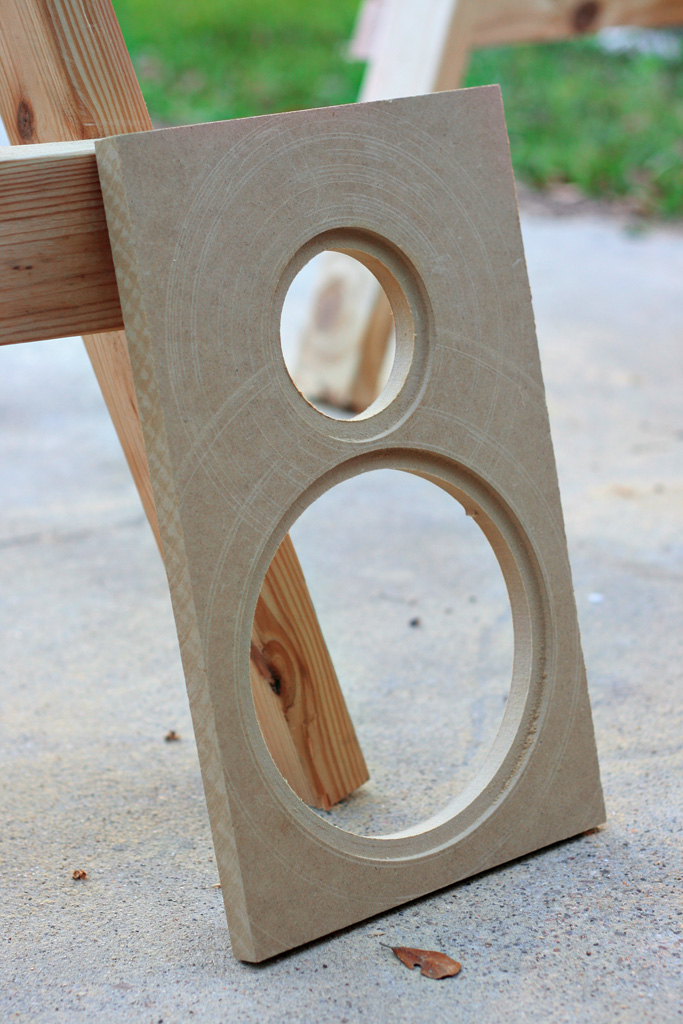
So here I am, out in the garage, doing one of the things I love best! It is literally an ideal spring day, with temperatures in the high 70s and a nice cool breeze. I’m out with my measuring tape, drawing lines and slicing wood panels with my circular saw. There’s brown aviator sunglasses on my nose, to protect against wood chips and the blinding Texas sun. A few mistakes here, a curse word there, and a course correction gets me back on track. By the day’s end I will begin to see the cabinets take shape, and there are very nice looking flush-mount circles cut with my new router for the drivers. This is a new skill I have learned today, seen in the lead picture at the top. A neat speaker cutting jig helped me get just the right cut. Using these new tools is gratifying.
Mid afternoon I uncap my water bottle and take a huge swig of the cool refreshment inside. Stopping to assess my progress, it’s uncanny how quiet and peaceful things are between the rounds of power tools. Birds chirp somewhere in the trees and the streets are empty. No one else is here, no one super into this the way I am. It feels like this instant is a triumphant moment, but without anyone else around who ‘gets it’ enough to chime in and say “oh man, what’s happening right now is so sweeeet!!” The absence of conversation feels both ironically strange yet somehow appropriate in an inexplicable way. Here I am, by myself in the garage, making it happen, “blowing it up” so to speak. I guess this sums up what it’s like being into niche hobbies, hey?
There’s a tiny bit of red sunburn on my neck and a mix of sawdust and sweat on my brow. I am in an odd mode of excitedly rushing to get to the next step yet leisurely configuring the power tools for my next operations. Occasionally a dog-walker goes by, curiously eyeing the piles of wood, my setup of sawhorses, and various power tools strewn about. Sporadic flocks of kids fill up the air with sound as they pass down the block. Now and then I hear the distant roar of a power saw from someone else’s garage. It’s a great day to get some work done. Maybe once an hour I stop and look around, conscious that I’m doing something I love, which I only get to do once every few years. Building loudspeakers is expensive. And time intensive. A whole lot of planning goes into picking the drivers, crossover points, cabinet design; this is sort of a sacred moment, The Moment Of Genesis when ideas begin to take physical form.
There may be no money, glory, or fame in it, but I have a lot of love for the speaker building art. I don’t think I could ever make a living off of it, even if I decided I was willing to risk it all to try. But I hope to build many more sets over the years, to share my love of high-fidelity sound, and help give to other people the experiences that their own DJing can give to themselves, with crisp detail in the playback.